The clinker capacity exceeded 64 million ton and cement capacity exceeded 105 million ton in Turkey with 48 integrated plants and 20 grinding stations as of 2010. If we consider the figures of 2009, Turkey is the biggest cement producer in Europe and the 5th in the world.
Safety
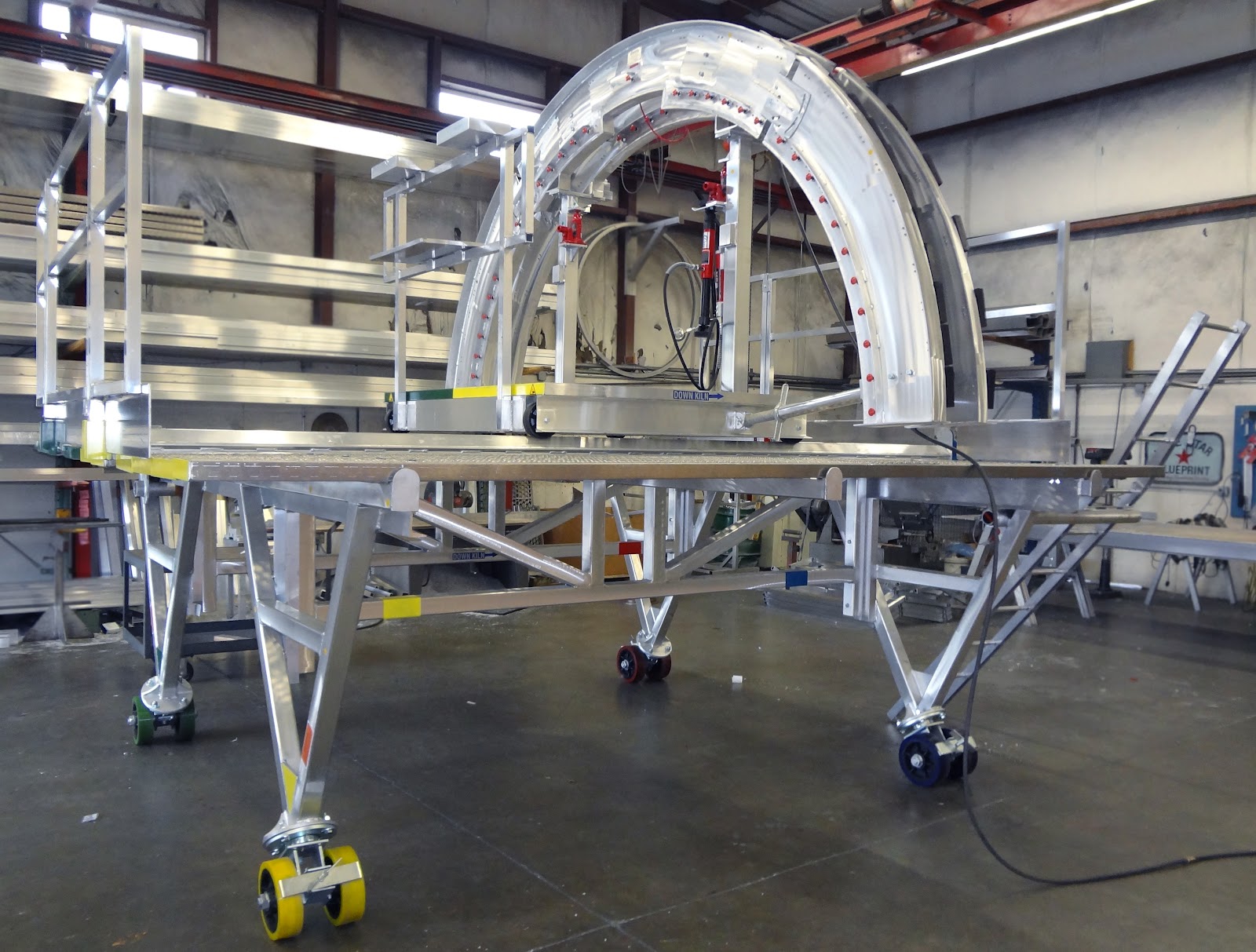
Somer International, an agent in Turkey has been representing many European Machinery and Equipment manufacturers focusing on the cement market; namely Pillard Feuerungen GmbH, Fives Pillard, Vecoplan, Brokk AB, Bricking Solutions, Di Matteo, Standard Industrie and HGH for decades. The most common point for all of them except focusing on cement industry is their perfect reputation in terms of quality product and problem solving business approach. They have started to cooperate with an American company, Bricking Solutions (a division of Brokk AB / Sweden). Their products include Brick Lining Machine, Safety Cages/Tunnels, Ramps etc. are made of high quality aluminum (6061 T6) and modern designs meets international standards for engineering fabrication and safety standards giving them a relatively high price upfront compared to steel products.
In the Turkish Cement Industry, it is not very easy to change their habits of using steel made (which is also an indication for strength) products with higher priced alternatives; but “thanks to Bricking Solutions patience and their professional business approach. They give very fruitful trainings in their factory for their agents” says Ahmet Somer the General Manager of Somer International who has successfully completed three full days training together with Ercument Ulguner the Product manager of Somer International. He mentions that increasing safety issues and the ease of use for this kind of products will increase the attention of the Turkish Cement Industry for
safety cages, safer and faster brick lining machines and Brokk remote control demolition machines. He also adds that the safety issues will be determining the type of product and process used in the cement industry more and more in the future. Some deadly accidents recently experienced will definitely speed up this change in the industry.
Alternative fuels
Another trend in the Turkish Cement Industry is to use Alternative Fuels. First one in AKCANSA/Buyukcekmece Plant (Heidelberg joint venture with Sabanci Group) was realized by Vecoplan. Vecoplan supplied the preparation (primary shredder, density separator, secondary shredder), conveying and the storage of RDF (Refused Derived Fuel). The plant is planning to increase the amount of alternative solid waste used.
Another group Cementir/Cimentas also made some investments in the Aegean region of Turkey for RDF preparation. Vecoplan also installed a TULS (Truck Unloading Station) for prepared RDF and a storage system to the CIMENTAS/Izmir Plant.
Finally a complete system to BURSA Cement; Primary Shredder 25 t/h, Magnetic Separator, Density Separator, Secondary Shredder 10 t/h, Storage and Vecobelt 160 mt (conveyor specifically designed for RDF transportation) and Automatic Sampling Station was installed by Vecoplan and running successfully by BURSA Cement experts.
Besides the RDF usage in some plants, the dried sludge was successfully used as an alternative fuel in NUH Cement. 70-80% wet sludge is dried down to less 10% and transported by a silobus to the system installed by Di Matteo. Dried sludge in the silobus is compressed to the silos and after the weighing system, pneumatically conveyed through the pipes and burned by a Pillard burner in the calciner. The
system capacity is 5 t/h.
OYAK Aslan Cement (previous Lafarge Aslan Cement) is another plant recently completed their investment for RDF and burning significant amount of RDF with their new generation Pillard burner, NOVAFLAM.
In the capital city of Turkey, Ankara BASTAS (Vicat Group) is another plant using RDF for many years.
Written by Ahmet Somer, the General Manager of Somer International