Kiln maintenance can take its toll on your bottom line. Plant managers need reliable, efficient maintenance methods to get back up and running quickly and minimize profit-stealing downtime. That requires using the right equipment — made from the best materials.
Bricking machines, suspended platforms, and kiln access kiln access ramps allow plants to safely speed up the refractory installation process, saving thousands of dollars in lost revenue. These useful tools are available from equipment manufacturers but can also be engineered in-house. Small differences in construction and materials can add up, though, so it’s important to thoroughly consider all options.
For many cement and lime producers, using their in-house engineers to construct kiln maintenance equipment made from steel is the go-to material because it is readily available. However, there are more efficient options available.
Lightweight, high-strength aluminum, for example, isn’t typically available and is rarely used in-house, but offers productivity and safety benefits that make it an ideal choice for kiln maintenance equipment construction. This material is as strong as steel and only 40% of the weight. This power-to-weight ratio leads to increased safety, productivity, and ROI.
Partnering with an equipment manufacturer that uses high-strength aircraft-grade 6061-T6 aluminum can be the best choice for your bottom line and your efficiency. Here’s how.
Faster Setup
The performance of a bricking machine or kiln access ramp during refractory installation is a manager’s top concern, where every minute the kiln is down is lost revenue. Setup and teardown times are equally important when it comes to overall productivity. Getting crews in and out faster requires a machine that is just as easy to put together as it is to remove once the job is done. Much of this comes down to construction materials: heavier materials — like steel — simply take more time and energy to erect.
For example, a steel kiln access ramp can take a full crew 6 to 12 hours to assemble, increasing downtime both before and after maintenance, which negatively impacts cost efficiency. The weight of the steel components also requires the use of heavy-duty equipment and complex hoists and rigging methods, increasing cost and risk of injury.
A similar ramp manufactured with lightweight, heavy-duty aluminum can be assembled in as little as 1.5 hours — depending on burn floor configuration — with a small crew and only light equipment, such as a forklift. Maintenance equipment that employs a modular design can further increase installation efficiency. These lightweight components can be transported into the kiln by just one or two men and can be quickly erected using pin connections, rather than nuts and bolts. By eliminating the need for extra equipment and manpower in the assembly process, aluminum ramps, bricking machines and suspension platforms increase productivity and safety while reducing overall costs with every setup and teardown.
More Durability = More Productivity
In addition to faster setup, plants will see increased durability from high-strength aluminum kiln maintenance equipment. With equal strength and significantly less weight, equipment manufactured with aircraft grade aluminum offers some of the highest load capacities on the market. Some custom-made bricking machines can hold as much as 6,000 kg (13,200 pounds) with an optional capacity upgrade, allowing them to easily handle three full pallets of brick. This is up to twice the capacity of the alternative steel machines — maximizing productivity without risking safety.
Industry-leading specialty manufacturers who incorporate high-strength aluminum into their kiln maintenance support equipment designs do so because of its increased load capacity over other metals. These companies use certified engineers and aluminum welders to ensure their products address the unique needs of each kiln site. The products are manufactured to international safety standards and are subjected to rigorous safety tests to ensure the materials and designs won’t falter even when working at capacity.
The result? Custom engineered bricking machines with a 3-to-1 safety factor. Crews with that kind of assurance can work with confidence knowing their bricking machine, kiln access ramp or work platform can comfortably handle heavy loads.
Greater Profits
When it comes to increasing efficiency during refractory installation — and in other areas of kiln maintenance — strong, lightweight aluminum equipment is an easy decision for plants looking to minimize downtime and get processing back on track.
Contact a Bricking Solutions expert for more ways to improve your kiln maintenance.
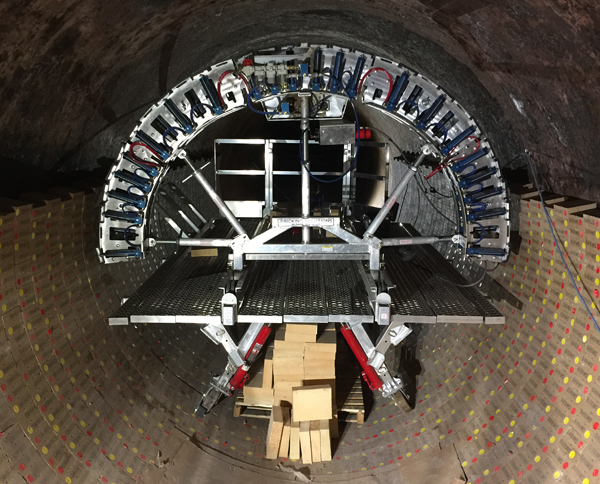
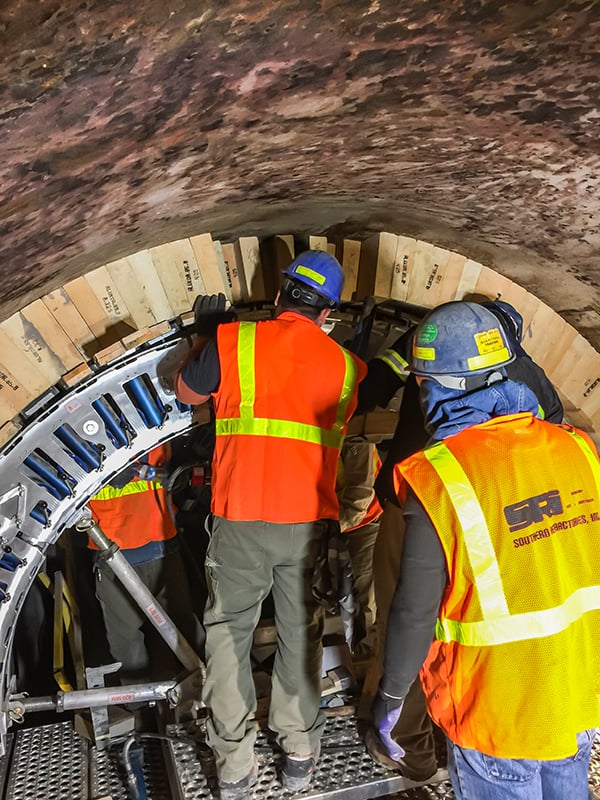