From burn floor to access, every kiln is unique. So, shouldn’t your maintenance solution be, too? Here’s how to select the refractory maintenance equipment — such as kiln access ramps, conveyor systems and bricking machines — that fit your operation and process to maximize your productivity.
Access
Metal access ramps have the strength and durability to get people and tools safely across the cooler, making them standard in facilities worldwide. Since every burn floor, cooler and kiln is unique, it’s a given that access ramps should be custom designed to ensure a proper fit.
The faster your ramp is installed, the faster your crew can get to work. So, to maximize productivity, look for a ramp with a modular design and lightweight components that’s easier to erect with equipment you already have on hand, such as a forklift. A well-designed, lightweight access ramp can be assembled in as little as 1.5 hours in many cases — that’s up to 40% faster than other aftermarket or self-built options.
But weight isn’t everything. Ramps must also be durable. Those made with 6061-T6 aircraft grade aluminum provide the best of both worlds — durable, long-lasting results at half the weight of steel. An access ramp manufactured with this material can support as much as 6,804 kilograms (15,000 pounds) live load. That’s as much as a fully loaded forklift.
Material Delivery
Brick management is another area where the right piece of equipment can maximize your productivity. It’s not always possible to drive into a smaller kiln to deliver brick, making brick management a labor-intensive process. In these situations, conveyors provide an efficiency-enhancing alternative that allows workers to move materials twice as fast and with less physical strain than by hand.
With a hydraulic conveyor, a two-person crew can bring a full pallet of brick into the kiln in less than 10 minutes. A roller conveyor would take a crew of five up to three hours to do the same. Look for a unit with modular components to allow for quick setup — as little as one to two hours, depending on the length of the conveyor and site conditions.
No matter the size of the kiln — large or small — minimizing brick handling leads to less material damage, increased safety and faster installation. With an incline conveyor, masons can move 15-20 bricks per minute from the kiln floor to the bricking machine with minimal effort. Again, a lightweight, modular design makes transportation and installation easy for a small crew, so look for a machine made with aircraft grade aluminum and easily maneuverable components.
Bricking
Finally, bricking machines are perhaps the best way to maximize productivity. An experienced crew using a bricking machine can install 1 meter (3.3 feet) of brick per hour, compared to roughly .6 meters (2 feet) with other techniques. However, since kilns come in a variety of diameters, it’s important to find a machine that fits your specific site if you want to optimize these benefits. Bricking Solutions offers a number of bricking machines to fit kilns from 1.2 meters (47 inches) to more than 6 meters (19.7 feet).
In addition to correct size, there are other characteristics that will provide greater productivity. A lightweight, modular design means faster setup so you can get to work quicker. A double arch system allows masons to start installing the next ring while the previous is keyed out for more efficiency. Additionally, look for a machine with an ergonomic cut-away keying section. This provides easy access and a clear view of the front arch for key brick installation to close out a ring.
Custom Solutions
When it comes to maximizing refractory maintenance productivity, partnering with an experienced equipment manufacturer will always provide the best results. Whether it’s an access ramp tailored to your specific site or helping fill in the gaps in your process with specialized clean up tools, our circle of refractory has you covered.
Contact our team today to maximize your maintenance productivity.
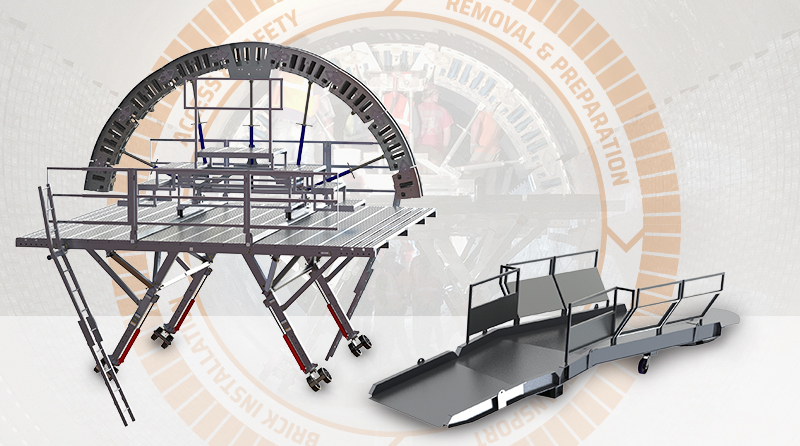