Selecting the Right Equipment to Optimize Refractory Safety and Productivity
Chris Jones, Bricking Solutions Lead Engineer
With refractory maintenance taking place annually in most facilities, making the right equipment choice not only increases productivity, it provides peace of mind in regard to worker safety. Throughout the entire process, from initial inspection to installation and final cleanup, these applications come with inherent dangers. To combat health and safety risks, contractors and facilities rely on specially designed support equipment that can stand up to the harsh conditions of refractory installation. But, just as site-specific evaluations must be made when selecting refractory brick, determining the specific support equipment for optimal results requires careful consideration.
To help make the selection process a little easier, here are four things facilities and contractors should consider for long-term safety and productivity.
1. Quality of Construction Materials
When it comes to selecting the safest refractory installation equipment, features like fall guards, railings, kick plates, non-slip surfaces and, where appropriate, stainless-steel netting are good indicators of a product’s overall safety contributions. However, contractors and facilities will benefit by looking a little deeper into the construction materials, as well.
Products built with high-quality materials will provide long-lasting service even in refractory installation’s harsh conditions. 6061-T6 aircraft aluminum, for example, offers an industry-leading strength-to-weight ratio. It also provides the durability of steel at a third the weight. Incorporated into modular designs, this results in equipment that is lighter and easier to assemble, reducing risk of physical strain. Additionally, the material’s strength can produce a high safety factor when combined with high-quality engineering.
When used in safety cages or personnel tunnels, for example, this material is strong enough to protect workers from debris up to 140 kilograms (250 pounds) falling from a height of up to 2.4 meters (8 feet), while still being light enough for two people to maneuver. A custom-engineered kiln access ramp using aircraft aluminum can support as much as 6,804 kilograms (15,000 pounds) live load, increasing protection for workers and equipment moving across the ramp.
2. Tailor-Made Options
Customization should also be a key consideration when evaluating refractory installation equipment for safety and productivity. Every kiln and burn floor offers their own set of challenges. Tailor-made equipment means site-specific concerns can be addressed in design, leading to a safer, more efficient solution. For many facilities, this is the main argument for using in-house engineers. However, a number of leading manufacturers also understand the importance of customization. Working with these companies can provide the best of both worlds — custom-designed equipment that safely meets the needs of a particular facility backed by the knowledge, experience and know-how of a specialty manufacturer.
3. Support Equipment for the Entire Process
Another important consideration for facilities and contractors to keep in mind is refractory installation is a long, multi-phase project. A number of products are available to help improve safety and efficiency throughout the entire process. A thorough investigation of the features and benefits of all available support equipment is the best way to ensure safety and efficiency through the whole process — from inspection to final cleanup.
The bricking machine is the most recognizable piece of support equipment for refractory installers. Originally designed to reduce physical strain and safety risks compared to more manual installation methods — like pogo sticks, mechanical jack screws, gluing, and jack and timber — bricking machines have evolved over the years to provide a number of cutting-edge safety benefits. The newest machines offer innovative features, such as adjustable dual-arch systems with pneumatic cylinders to push bricks into place, greatly reducing the risk of injuries from unsupported material overhead. Ergonomic design elements further increase worker comfort and safety. Some models also offer a cut-away section for unobstructed access to the keying area to increase ease and visibility for closing out a ring.
However, to truly optimize refractory installation safety, contractors and facilities should consider support equipment beyond just bricking machines. Certain manufacturers specializing in refractory installation have developed entire product lines that increase safety and efficiency throughout the whole process. From safety cages and access ramps to hydraulic and incline conveyor systems that allow workers to move materials twice as fast as manual methods with significantly less physical strain, these manufacturers offer a number of equipment solutions that facilities and contractors should keep in mind.
-
Long-Term Manufacturer Support
Regardless of who manufactures a facility’s refractory equipment, ensuring long-term safety requires continual training and maintenance. While the majority of this upkeep falls on the facility or contractor, things like on-site equipment inspections, and parts and service from a reputable manufacturer are worth considering to make lasting safety more attainable.
If possible, look to partner with a manufacturer or dealer that offers on-site inspections. These visits can often be turned into learning opportunities for plant personnel and contractors. Over time, crews change, and those on hand for the initial commissioning — where assembly, maintenance and storage requirements were originally outlined — may not be the same faces three years later.
Additionally, a lasting relationship with the manufacturer for parts and service support helps ensure equipment is ready for operation during unscheduled kiln downtime.
Safety Conscious
When it comes to refractory installation safety, making the right equipment choices can lead to long-term success. Partnering with industry-leading manufacturers that specialize in refractory support equipment provides an unparalleled wealth of knowledge and experience, as well as innovations that continue to meet the industry’s evolving safety needs.
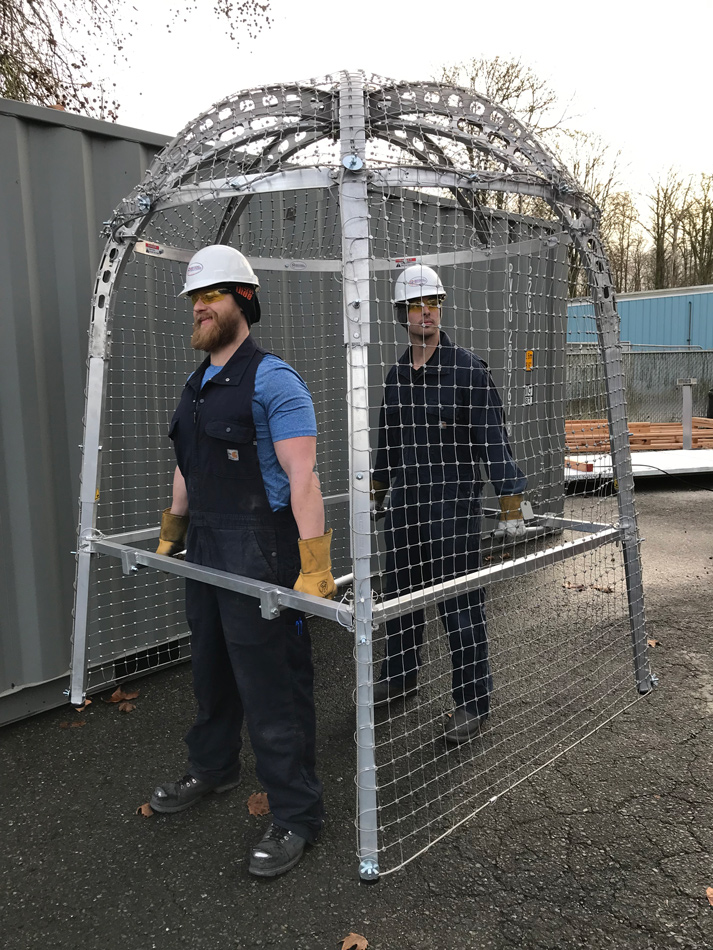
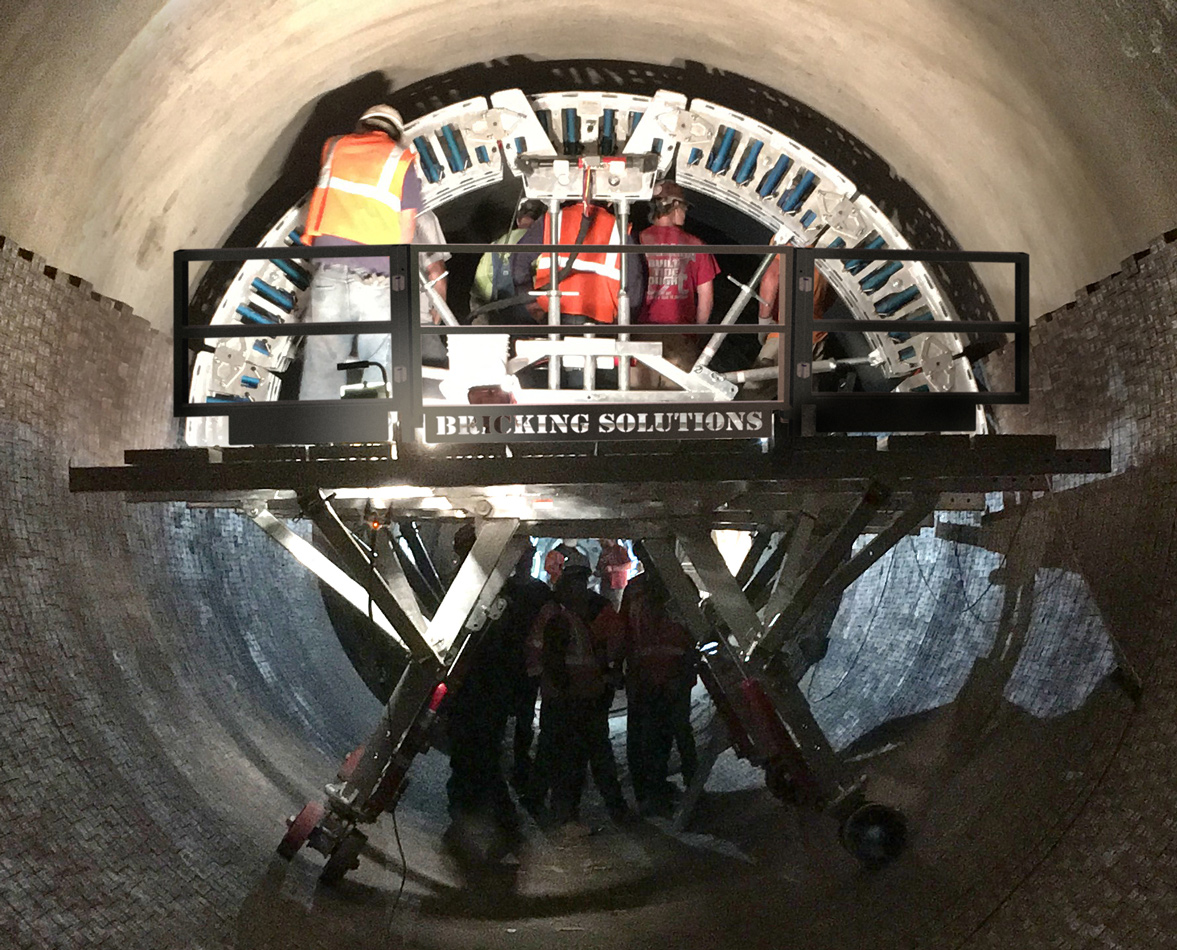
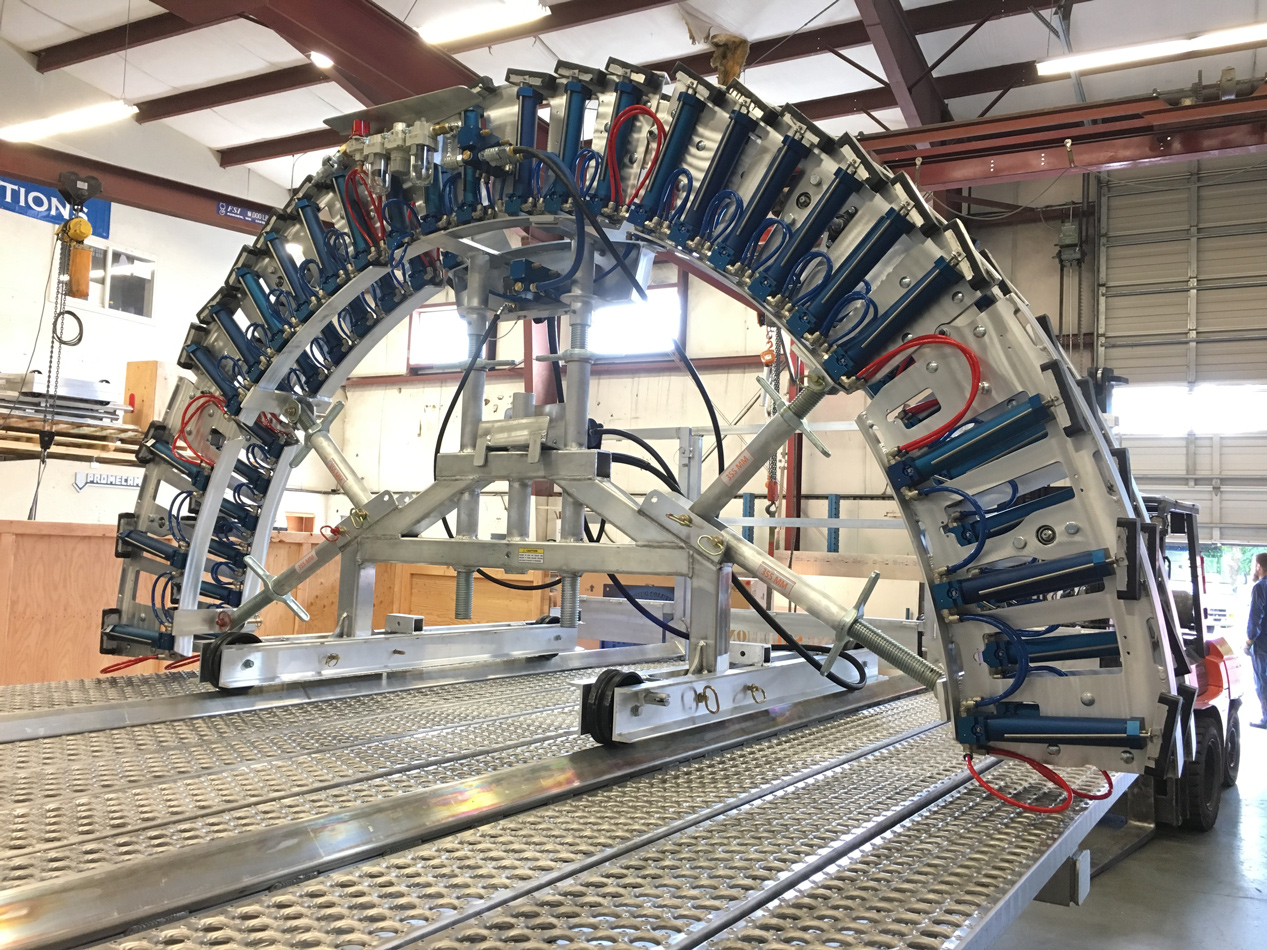
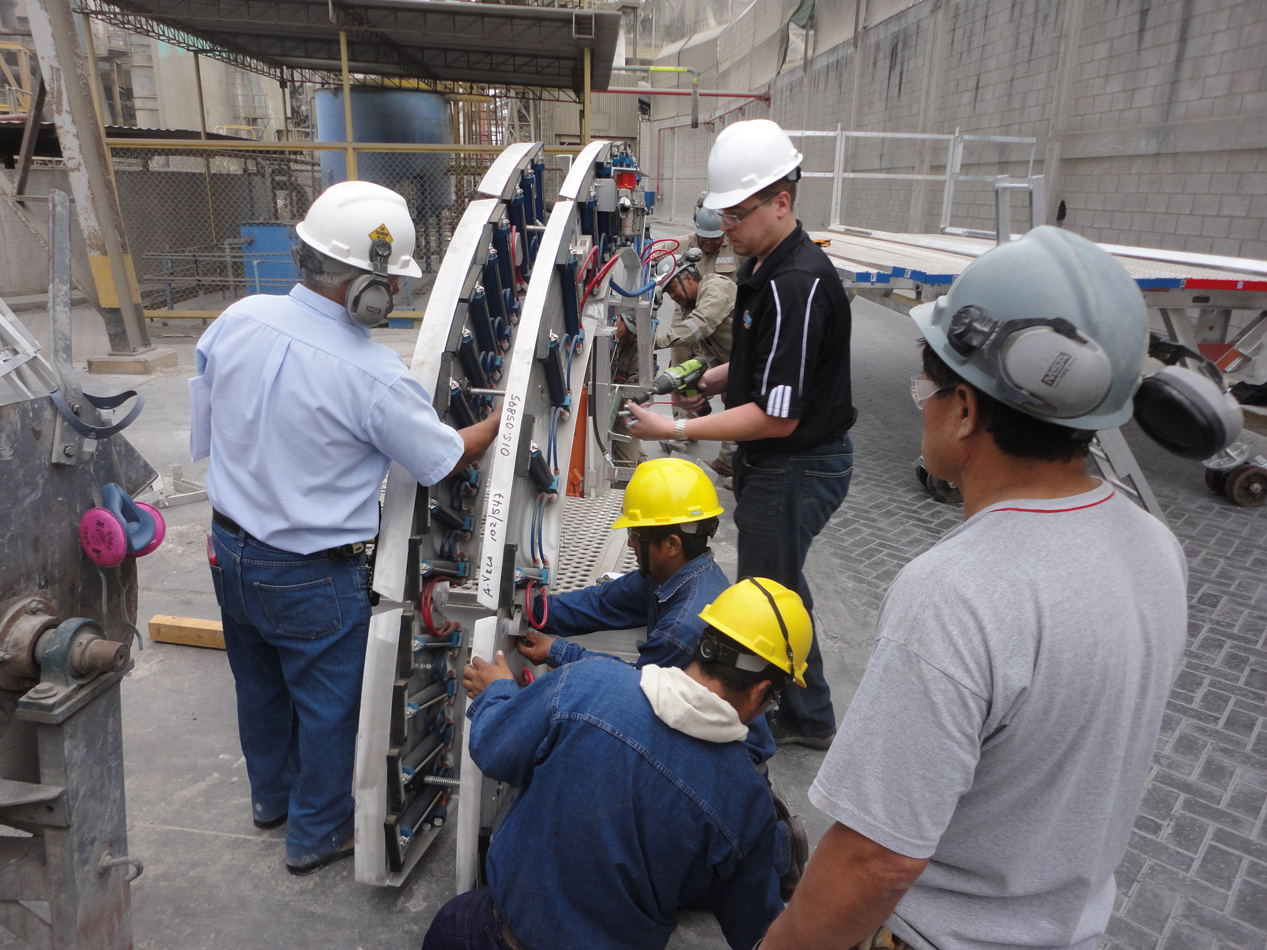