When to Repair or Replace Your Bricking Machine
Equipment investment is always a numbers game. Having the right tools on hand at the right time is imperative for efficient operation. But does it need to be a brand-new machine? Or would repairs to key components provide the same productivity and safety with a smaller investment? And what flexibility does your choice provide? Is there enough in the budget to upgrade to the latest model, or would it be better to use the capital expenditures budget for repairs this year?
When it comes to high-quality bricking machines, like our EX Flexx50, durability and longevity can make the repair versus replace decision even harder since, with proper maintenance, these machines can operate safely and efficiently for decades. Eventually, though, it’s a decision that will need to be made.
Whether repair or replacement is best for your operation can only be determined on an individual basis, taking into account the condition of your bricking machine and the unique needs of your business. However, here are some key areas to consider as you crunch the numbers.
How Old is Your Machine?
While a bricking machine from a reputable manufacturer can easily stand the test of time — even in refractory installation’s harsh conditions — age is the first consideration facilities and contractors should evaluate. The number in itself might not tell you if repair or replacement are required, but, like any piece of equipment, there are certain safety inspections that should be conducted based on age and use.
Carefully evaluate bricking machines after each use, and initiate an in-depth, on-site inspection from the manufacturer at least every three years or five uses. After eight years of use, inspect bricking machines annually to ensure safety and overall condition of the equipment. These evaluations should include a visual inspection as well as dye penetration tests on all welds. Depending on the model, the technician should also check additional features, such as valves on machines with pneumatic cylinders. As part of our aftersales services, Bricking Solutions offers equipment safety evaluations on-demand, which is highly recommended for older machines. The inspection results will provide a strong basis for objectively evaluating the cost of repairs versus replacement.
Other considerations to keep in mind are safety and productivity upgrades that might be available with newer models. Innovative, new technology, such as adjustable dual-arch systems or ergonomic design elements, for example, will increase employee safety and comfort. Upgrading an existing machine with new technology may be considered a repair in some cases, but, at a certain point, replacing an older machine with the latest model will provide a better ROI.
Body Damage
For models showing their age, or those that fail the dye penetration test, replacement is usually a more cost-effective solution.
Whether your rig is made from lightweight, high-strength aluminum or another material, re-welding decreases overall integrity and should be limited. If the dye penetration test uncovers several damaged welds, replacing the machine is the only way to ensure long-term safety.
On the other hand, repair is more cost effective for minor body damage, like a bent panel. Here’s where working with a manufacturer really pays off. OEM bricking machines with a modular design allow for easy replacement. Just contact your manufacturer, and a new part is quickly fabricated to your rig’s exact specifications. Installation is a snap, allowing your team to get to work right away.
This process requires some lead time but is virtually hassle free compared to reverse engineering a rig designed and built in house. And, by contacting your manufacturer for replacement parts right away, even this hurdle is easily avoided.
Safety and Productivity
Additionally, refractory installers should consider the overall safety and productivity their bricking machine provides.
An unsafe machine should be replaced immediately — full stop. It’s impossible to put a price on workplace safety and potentially put employees in danger.
However, if it’s just a single component that’s not working properly, such as a pneumatic arch cylinder, a simple repair is probably all you need to get your machine operational. Like any piece of equipment, bricking machines have parts that need replacing from time to time. Your in-house team can easily complete many of these repairs – if they have the right parts.
Stocking common wear parts minimizes unnecessary downtime and keeps shipping costs down. Some equipment manufacturers offer inventory assistance to help you determine which components to keep on hand for your specific unit.
Making the Call
The decision to repair or replace is not always an easy one, and, ultimately, the answer depends on your specific situation. Thankfully, OEMs like Bricking Solutions offer onsite evaluations to assist in making the replacement decision. To schedule an evaluation or discuss your repair and replacement options, contact our team today!
Repair or Replacement Checklist
Repair is likely an option if:
- The machine is less than 8 years old and has been maintained according to manufacturer recommendations.
- The machine remains structurally strong.
- Repairs are limited to a single component, like the pneumatic system.
Replacement is required if:
- The machine is 8 years or older and dye test shows failing welds.
- The machine has cracked welds.
- The machine would be unsafe even with repairs.
- New technological advancements offer enhanced efficiency effectively offsetting the additional costs.
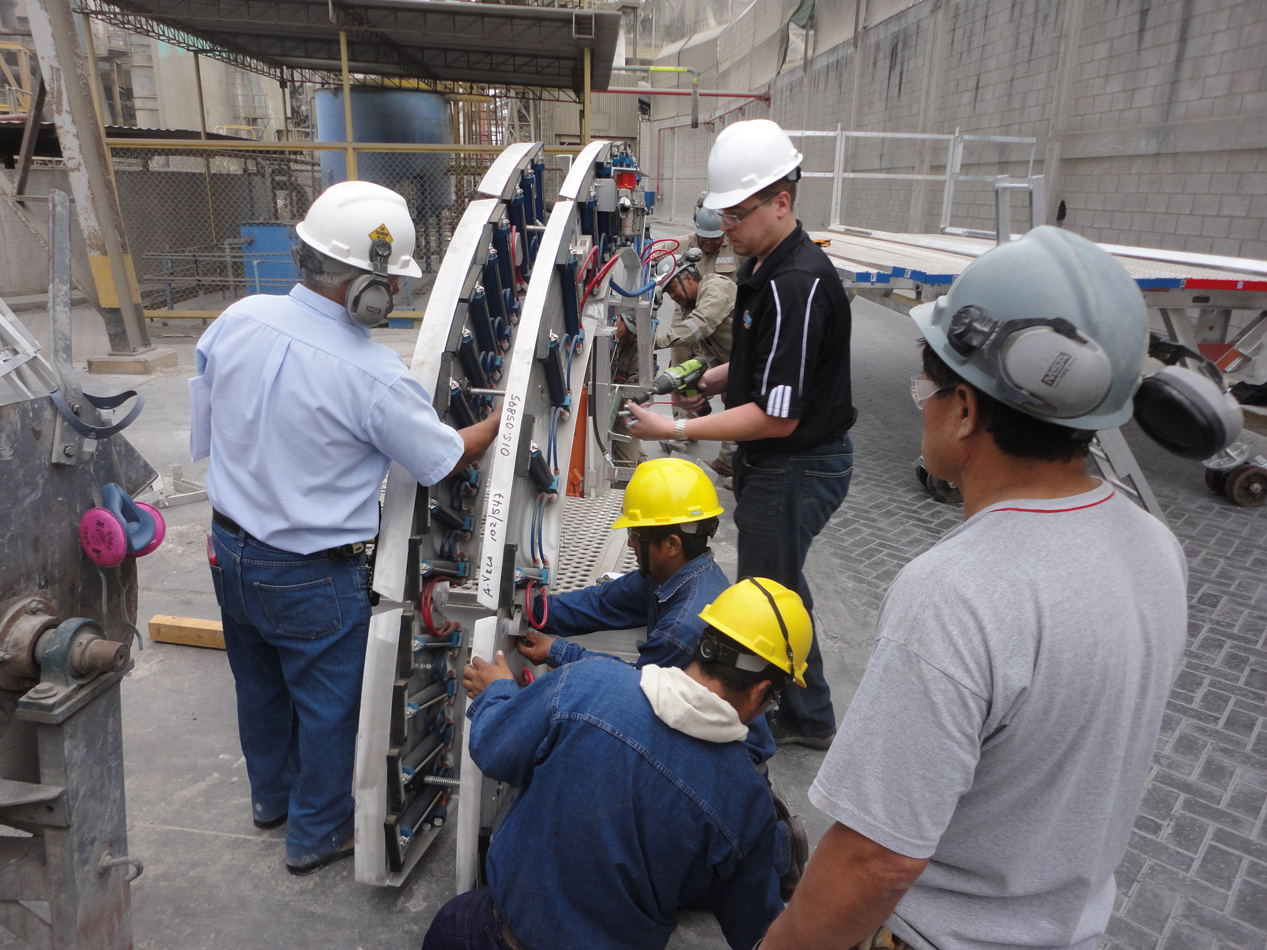
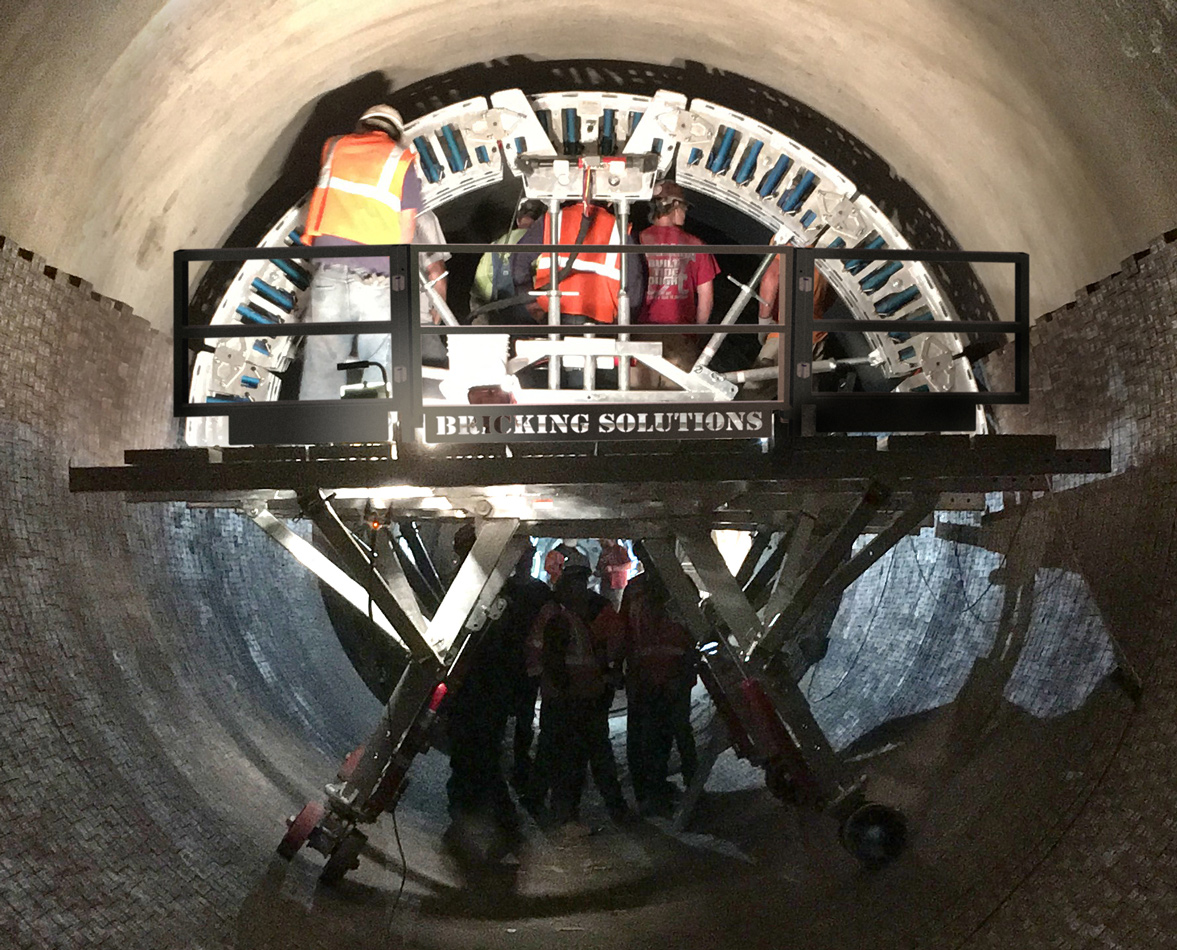