Refractory maintenance in a metal processing facility is already a big project, which only gets bigger when the furnace in question is 40 feet tall and 22 feet in diameter. In 2014, Dave Drorbaugh II worked as lead project manager at a metal processing facility. That year, they initiated a major shutdown to rebrick half of their furnace, which was just that size. Time was tight, so the team decided to go with conventional scaffolding built off a hanging static platform for access. The scaffolding system got the job done, but Drorbaugh and his team knew there were safer and more efficient options.
A decade later, in 2023, the facility hired RECON Engineering & Construction for a full shutdown of the same smelter. Drorbaugh, now a business unit manager at RECON, and his team partnered with Bricking Solutions for a custom EZ Lift Platform to get the job done faster.
2014
The original rebricking project Drorbaugh worked on in 2014 only required the removal and installation of the lower half of the furnace shaft — which is why scaffolding was a possibility. Only two layers of scaffolding could be used reliably before the platform started to sway and deflect. Adding any additional height or weight destabilized the structure, making it unsafe for crews.
The scaffolding system also required multiple shifts to set up due to a variety of pipes, hardware, boards and other materials that needed to be set up. Similarly, breaking down the scaffolding became an issue. The sections of the scaffolding needed to be both brought in and removed through a 1-by-1-foot port. Removing the scaffolding that way would delay the project and result in a six-figure production loss. In the end, they decided to leave the framework in the furnace and melt it away.
Because the unit has a life cycle of 8-10 years, the wait between rebuild projects means each shutdown is a new challenge. Each shutdown, the team completing the project needs to consider new technology and methods while remembering the lessons from the prior rebuild.
“Scaffolding really became our only option 10 years ago. But we had a lot of logistical issues,” Drorbaugh said. “It became something of a loose end. But, with a longer timeline and a larger repair scope, RECON decided to look for a safer, more viable option for the 2023 shutdown.”
2023
The RECON team wanted to take full advantage of the longer project timeline. The extra time meant they could seek out a safe, stable custom-built equipment platform. Prior experience and research led them to Bricking Solutions, a manufacturer that could provide full specs and an official rated capacity for any platform it engineered.
Bricking Solutions custom engineered a 24-foot-diameter (7-meter-diameter) suspended platform for the project.
“We were looking at ways we could potentially improve upon what was done 10 years ago, something faster and quicker that facilitated parallel work fronts, that sort of thing. From a safety standpoint, the suspended platform was a turnkey engineered solution instead of something homegrown. We were able to purchase and roll it out,” Drorbaugh said. “We submitted this product in our use plan for approval. Because there was documentation and it came on letterhead, it made the approval process more straightforward and gave our team the confidence to get to work.”
Suspended platforms often need roof prep, but the facility already had a framework in place. The RECON team simply set up the support beams and tacked them down. The EZ Lift Platform, made of high-strength 6061-T6 aluminum, offered the same strength as steel at a third of the weight. More importantly, modular construction made it easy to assemble in just three hours.
The Project
Before assembling the platform, however, RECON worked on the demolition of the refractory lining with Brokk demolition machines before scaling the shaft clean. The mechanical crew then started rebuilding the shaft. The hearth included three layers of brick while the shaft required only one layer of refractory brick and one layer of ram.
Halfway through rebuilds, RECON put together a temporary bulkhead on which they could assemble the suspended platform. RECON positioned the platform high in the shaft so the demolition and reconstruction could be completed below. They used six rented hoists to move the platform in the shaft. Once the team could move the platform reliably, they dropped out the bulkhead so the bottom third of the shaft could be completed.
Work Fronts
Once the demolition of the bottom third of the shaft was completed, RECON’s crew of six worked on the platform preparing the shell steel and rebricking the upper half of the shaft while multiple construction teams worked below the platform — a simultaneous work front tactic that was a major selling point for RECON. The RECON team completed the shell work with rivet busters and needle gun scalers. They paired the EZ Lift Platform with a Bricking Solutions Material Transfer Basket to raise and lower brick safely. An additional hoist was set above the platform to raise and lower the basket. The team installed more than 2,000 tons of material for the furnace refurbishment with 260 tons of material in the shaft.
RECON then rebricked the interior of the shaft. They needed to keep the weight on the platform below 4,000 pounds, so they limited the brick on the platform to 1,000-pound (454-kilogram) increments.
Once the brick installation at the top of the shaft finished, the mechanical crew and RECON’s team switched places. “The suspended platform allowed us to facilitate multiple work fronts and worked as a support for the mechanical and structural work at the top of the shaft once we moved to refractory work on the hearth,” Drorbaugh said. “While the platform started out being used for the refractory installation team, it ended up being a work platform for various mechanical and structural crews that needed to work up top, too. In fact, to make sure we weren’t interrupting the workflow of the mechanical crew, we left the platform set up in the shaft for an additional month after rebricking finished before lowering it down and disassembling the structure.”
The RECON team took apart the suspended platform and removed it from the furnace by hand over a single shift change, minimizing any impact to ongoing work. RECON estimated that the teardown time was about one-fourth the time scaffold might require. The custom-built EZ Lift Platform and Material Basket were such a success that the base metal processing facility kept the equipment for use in future shutdowns.
“On the tactical level, the EZ Lift Platform is a big success, both in terms of project logistics and safety needs,” Drorbaugh said. “The Bricking Solutions team remained in contact and ready to answer any questions throughout the project. Thankfully, with the onsite training Bricking Solutions provided, we didn’t run into any structural issues with the platform and the rebricking proceeded nicely.”
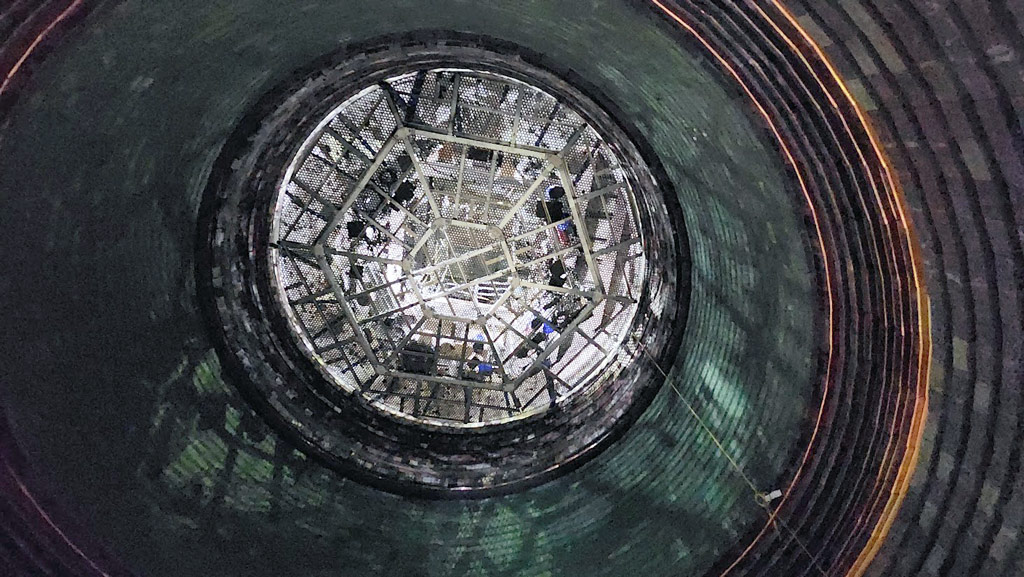

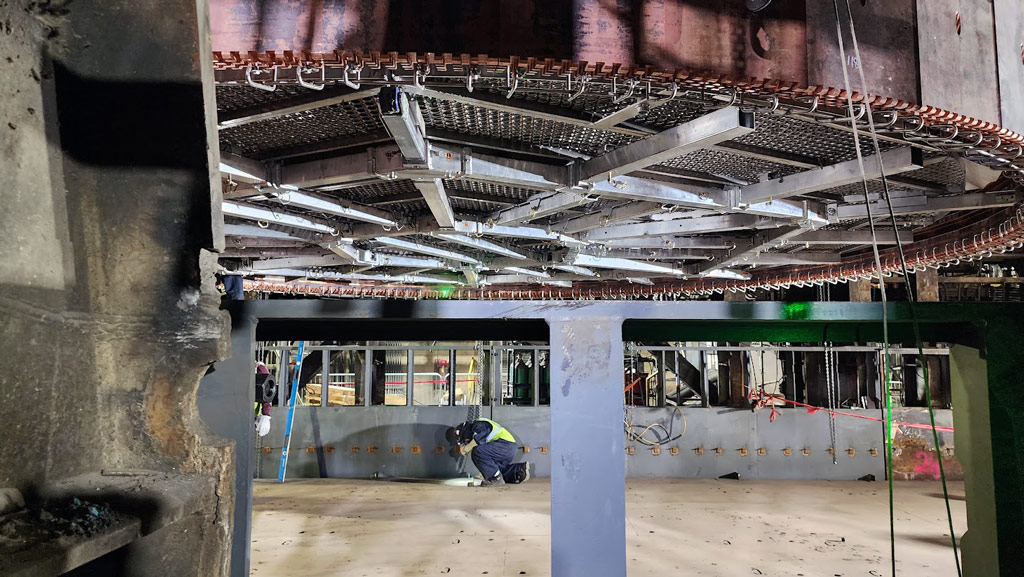
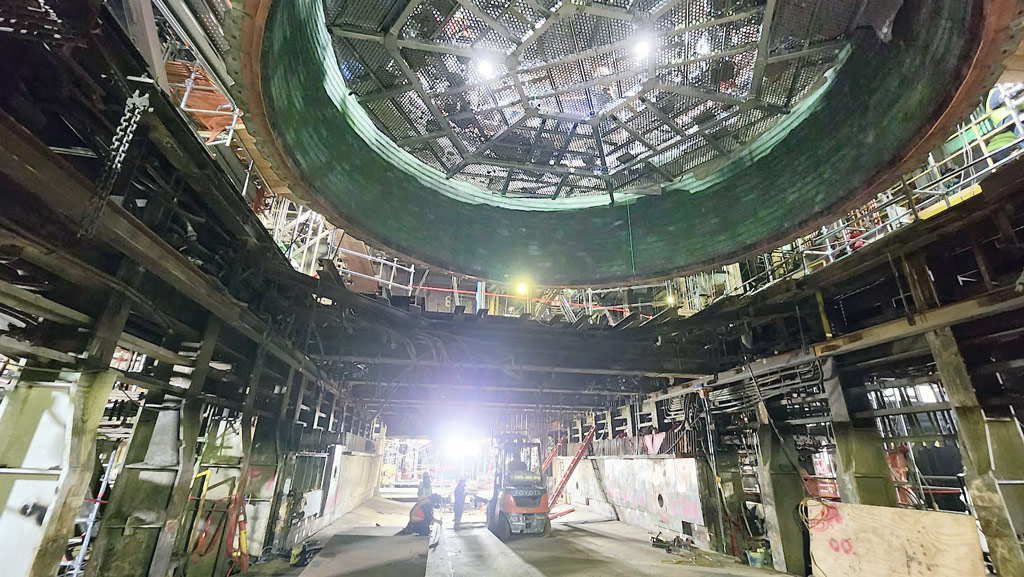