Refractory brick testing is an important factor in determining when brick replacement is required for furnaces, cyclones, kilns and other vessels. Having a monitoring device on hand makes the process easier, giving operations the ability to check brick thickness whenever downtime occurs.
Brian Robert, process engineer at the Stockerton, Pennsylvania, facility of Buzzi Unicem USA, one of the leading manufacturers of cement in the United States, uses a refractory brick measuring device any time the cement kiln is down for more than a day, which typically happens a couple of times a year. When the facility’s Linometer, a device that has since been discontinued, showed signs of wear, Robert reached out to Bricking Solutions for a replacement. Bricking Solutions provided Robert with BrickCheck, a refractory measurement device with capabilities similar to the Linometer.
Calibration
Robert used BrickCheck during the shutdown of their cement kiln. The device came with a control unit, measuring probe, connecting cable, anti-dust cover, carrying case, plastic case and instruction manual.
Bricking Solutions recommends drilling one hole in the refractory to help calibrate the device to within 0.1 of an inch. This allows a physical and digital measure of the brick and gives operators the ability to measure the holes for themselves. Typically, drilling is used in preheater towers. Some facility managers trust the drilling method more than a digital readout, even though the drilling damages the brick of the kiln. However, Robert didn’t feel drilling was necessary for what he intended. He compared the brick readouts to the full thickness brick against the kiln shell to determine accuracy, which came out within a quarter of an inch.
Use
BrickCheck uses electromagnetic measuring through the eddy currents principle to determine brick thickness. The magnetic probe is placed against the brick, and the 4-digit display shows the measurements in centimeters. The probe and telescoping extension arm give the operator a full range of motion, allowing them to measure the entire circumference of the vessel without bending, stretching or stooping.
“BrickCheck allows us to quickly measure brick thickness at multiple points in a ring of bricks,” Robert said. “This makes it easier for us to determine how many feet of brick we have to take out and re-install.”
Robert found the controller informative and easy to use. The backlighting on the controller made it easier to read the screen since it was bright and clear. And the readouts can be exported to a computer. While Robert didn’t use that function, he could see it being useful for someone performing measurements by themselves without a notetaker available.
“I’ve used other, similar devices in the past, but BrickCheck has some more modern capabilities regarding data and the display,” Robert said. “The main benefits I saw from this device is that it offers faster brick measurement with a reasonably friendly user interface.”
Final Thoughts
BrickCheck is made to quickly measure the brick thickness at multiple points in a ring of refractory. Operators can use the knowledge gained to see what the normal wear rate is for each vessel in the facility and how that rate varies over time. This can give operators enough information to notice hotspots or abnormal brick wear when conducting regular brick measurements.
“Overall, I think BrickCheck accomplishes the goal of providing accurate and precise brick thickness measurements. I believe that this tool could be a useful asset to any cement plant to help provide useful data when speed and multiple measurements are needed,” Robert said.
To learn more about BrickCheck and how it can be used in the vessels at your plant, contact us today.
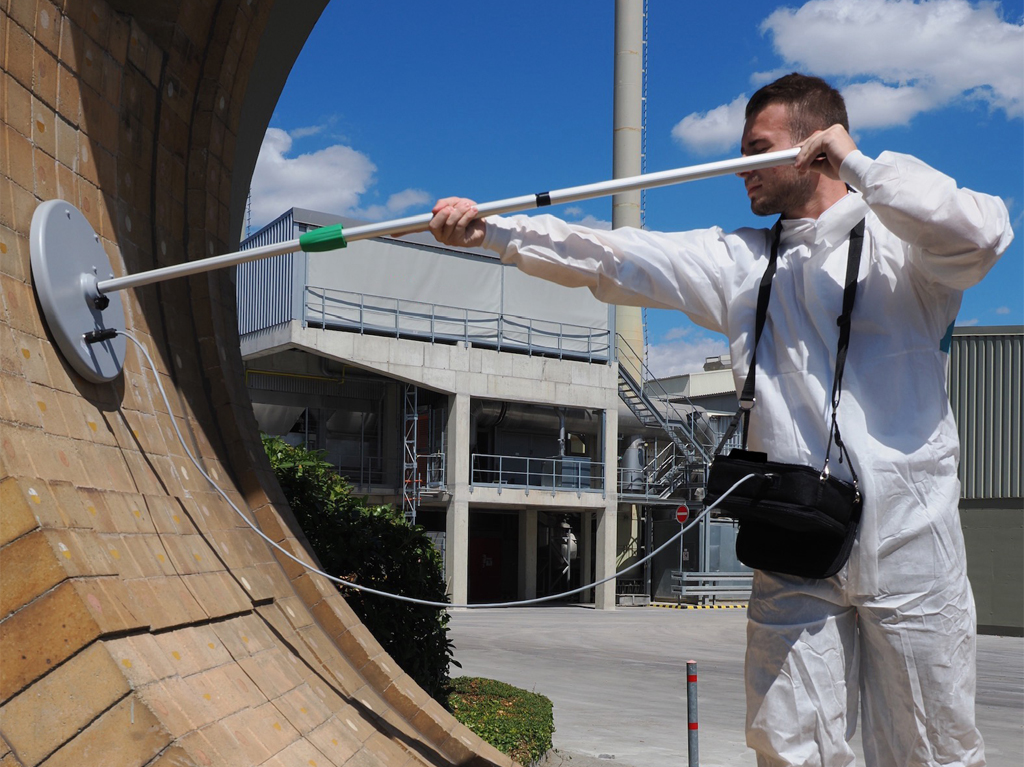
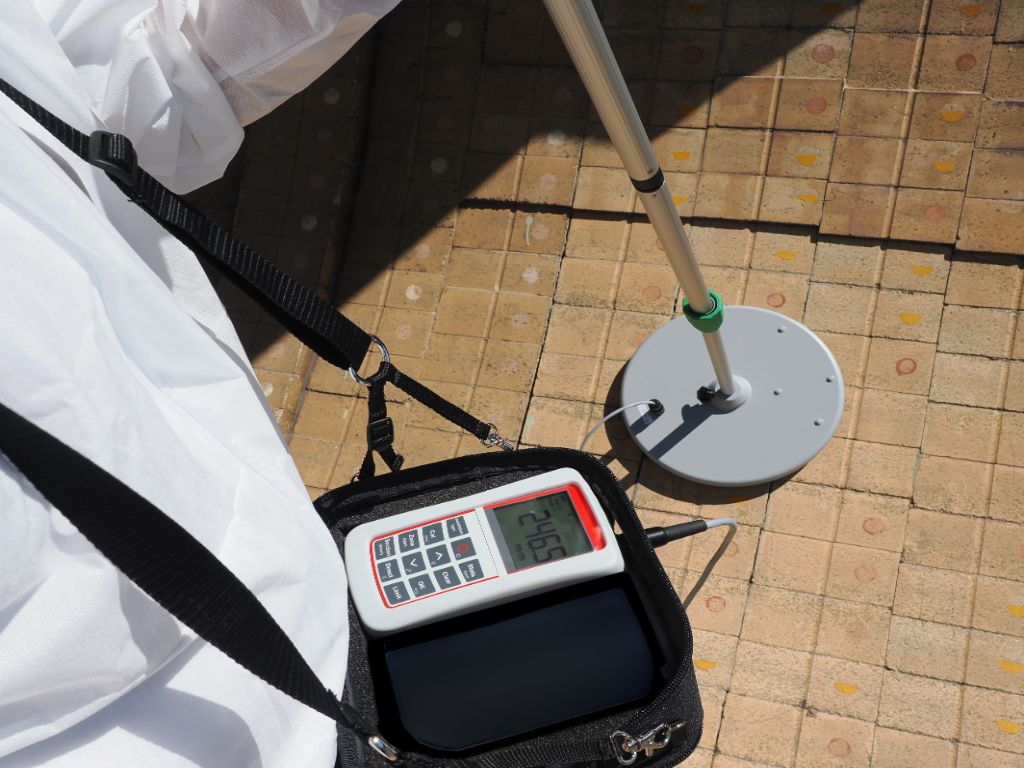