Suspended platforms are game changing when you have vertical vessels to maintain. They eliminate the lengthy setup times and safety risks that come with scaffolding. One of our customers, a sugar beet processing facility, could only complete a fraction of the major repairs needed when working for the full length of their maintenance cycles — two to three months — using scaffolding. Adding an EZ Lift Platform made maintenance faster and easier, allowing them to complete their work in just eight weeks. In another case, a cement plant saved five full days — not shifts — of labor installing a new thimble in a cyclone. Based on a $15,000 per hour shutdown cost, that is a savings of about $1.8 million.
The suspended platform does require some initial site preparation. But once that is completed, the modular design and pin-together connections streamline installation.
We’ve answered some of the most common questions we hear about installing a suspended platform. Keep reading to learn more about adding one to your plant.
1. What kind of site prep is needed for a suspended platform?
The first thing to know is that the platform components will be delivered to your plant in heavy duty crates to protect them during transit. If the installation isn’t going to take place immediately, be sure to arrange a safe area for storage. As an additional option, the platform can be organized on custom aluminum storage racks. This allows the racks to be easily lifted via crane to the main staging area where the platform will be assembled.
One of key features of the EZ Lift Platform is that it is designed so that its individual structural components each weigh less than 18kg (40 lbs.) and will fit through a 560mm (22 inch) diameter opening. The only exception to this is the hoists, but they will still fit through the same size opening.
Working in conjunction with Bricking Solutions, a decision will be made regarding whether a temporary floor needs to be installed or if the platform can be assembled at the base of the vessel. For vessels like cyclones or calciners, expect to have to install a floor. Vessels like copper smelters would need to have the slag leveled — and cooled — so that the platform can be assembled at the base.
For vessels with a roof (i.e. cyclones), 6 holes will need to be bored through the roof at 60° increments. Positioning of the holes is determined by location of the main access door and any structural elements in the roof. Threaded pipes are inserted into the holes and welded in place to become a permanent port. It is through these ports that the steel ropes will be dropped through to suspend the platform.
2. What can be done for structures without roofs?
Beams can be used to support the platform if the structure doesn’t have a roof. This method will require that ports are cut into the sidewall of the vessel. The plant is required to ensure the sidewalls of the vessel can support the load before installation takes place. The rated weight should be around 8,000 pounds (3,628 kg) with a 4:1 safety factor. We offer telescoping beams that ease installation processes and ensure proper load rating and safety. These beams are segmented and specifically designed for the vessel. They’re easier to maneuver than full-length beams and can be used at the bottom of the vessel to support a deck for platform assembly. A “shoe” also is included with the purchase, used to keep the beams horizontal while they’re being installed throughout the vessel.
3. What safety features does the suspended platform have, and how can we make sure installation is safe?
A safe installation requires diligence both in terms of training and safety. Before installation, our experts train crew members until they are deemed a ‘Competent Person,’ which allows them to train others in the facility. These individuals will be trained in proper installation practices.
Another way we increase safety is by ensuring our products are made from the highest quality materials. The suspended platform is made of lightweight, 6061-T6 high strength aluminum that is as strong as steel but weighs 40% less. The planking materials are made of aluminum Perf-O-Grip with non-slip surfaces. All materials included in the suspended platform package comply with Multipoint Suspended Platform safety regulations, including regulations from OSHA, ANSI, CSA and EN.
Plants are responsible for ensuring safety standards are met in the facility. This includes ensuring that the roof will be able to support the platform’s load.
For installation, we require, as per standards, wire rope anchors with a 6:1 safety factor that are rated for 1,500 pounds (680 kg), along with 6 hoists rated for the same weight and electrically insulated cables. Additional safety features that can be added are outer and inner fall guards and material hoists with ratings for around 1,000 pounds (450 kg).
Making the Switch
Switching from scaffolding to a suspended platform for maintenance requires initial planning, but Bricking Solutions works with you to make sure the installation process goes as smoothly as possible by providing detailed installation instructions. Facilities that have made the switch save thousands of dollars every maintenance cycle and have seen immediate returns on their investment. Contact us to learn more about suspended platforms and how they can improve efficiency in your plant.
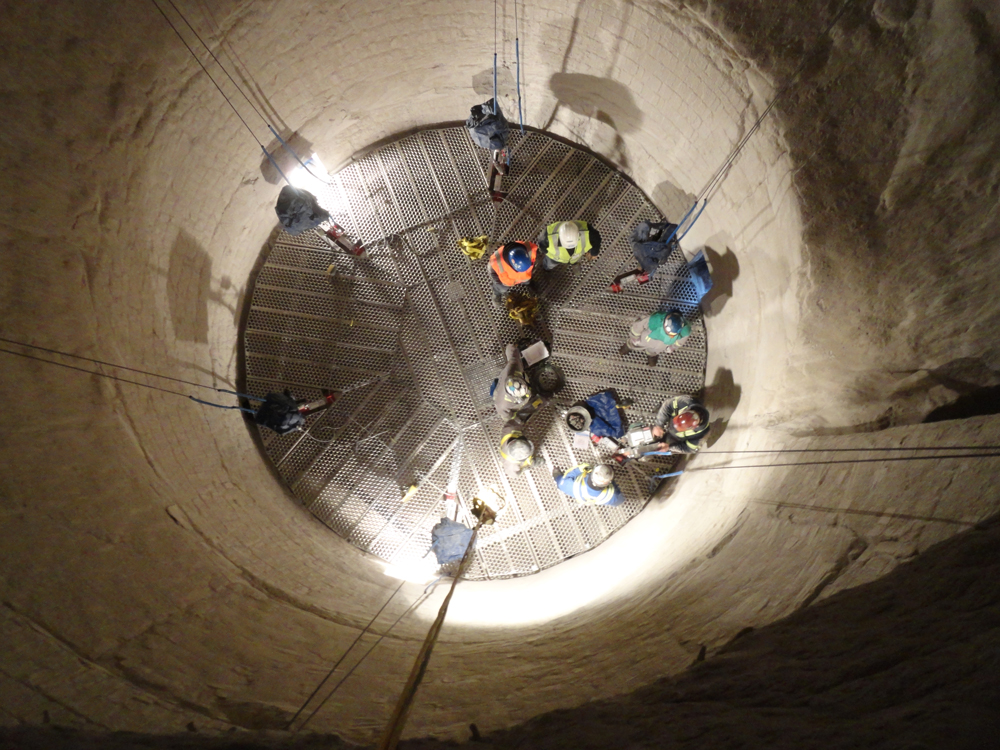
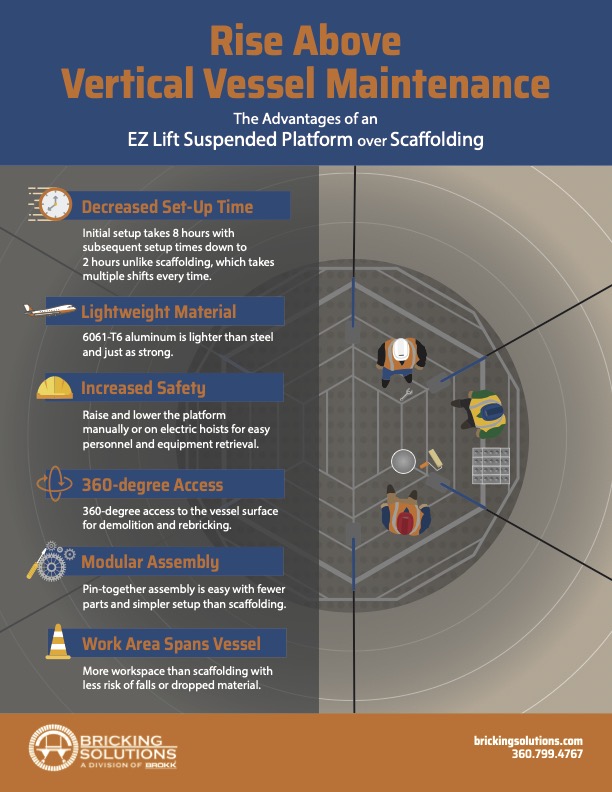