Kiln access ramps are the first equipment on site and the last to be removed when refractory maintenance is complete. They provide the only access across the cooler for crews, equipment and materials. They also have a significant impact on both productivity and safety.
Working with an OEM for a custom kiln access ramp offers a number of benefits for more efficient refractory maintenance. In addition to a design tailored to your specific site, a custom ramp can provide faster setup, which means your crew can get to work more quickly. Here are the top three ways custom ramps can benefit your operation.
1. A Perfect Fit
Each burn floor, cooler and kiln present unique obstacles, such as pillars, burner rails, air ducts and piping. Because of this, each access ramp should be specially designed to ensure a proper fit for optimum efficiency, portability and safety.
Working with a custom manufacturer for a tailor-made kiln access ramp gives you flexibility to incorporate the features that will make your process most productive. A cement plant in Chile, for example, needed to be able to install the nose portion of the ramp – the piece that goes from the bridge to kiln – by hand while still maintaining maximum capacity.
Off-the-shelf ramps might be quicker to fabricate, but they fail to address the individual challenges of each facility. From approach angle to threshold height, custom-made access ramps are engineered to fit the specific parameters of the project with precision and forethought that increases maintenance productivity and safety.
2. Fast Installation
In addition to extensive experience solving challenging access ramp needs, OEMs have access to unique construction materials and techniques that result in faster assembly. This saves significant time during setup and teardown — up to 80% in some cases — increasing overall refractory maintenance efficiency.
Look for a ramp manufactured with high-strength 6061 T6 aluminum. This material is as durable as steel but at one-third the weight, resulting in a lightweight ramp that’s easy to maneuver with basic support equipment. Ramps constructed from this material will support as much as 15,000 pounds (6,804 kilograms) live load and offer a 3:1 safety factor. Some can be assembled in as little as 1.5 hours, depending on ramp length and burn floor configuration, compared with 6-10 hours for steel ramps. In addition, the material is corrosion-resistant without secondary treatment.
For the best user experience, work with an experienced manufacturer. This ensures that your ramp is properly engineered for your application, making installation faster and easier.
3. Increased Safety
It goes without saying that a ramp tailored to your unique site will provide safer access to your kiln. Many custom-engineered ramps incorporate standard safety features, such as curbs and fall guards, to protect workers as equipment moves across the ramp.
However, a custom access ramp allows you to take safety even further. For example, a cement facility in South Carolina needed to safely transport materials using a narrow ramp. Including a 406-millimeter (16-inch) curb guard on its custom-engineered access ramp meant there was no risk of accidentally driving equipment over the edge and falling into the cooler. Some OEMs also offer accessories like safety cages, personnel tunnels and accessories that integrate seamlessly with their ramp designs. These protect workers on the bridge section of the ramp from castable falling from the hood.
Optimize Your Process
An effective refractory maintenance process requires efficiency in every step, including kiln access ramps. Year after year, a custom-engineered ramp system allows maintenance crews to get the job done safely and efficiently, ramping up productivity and optimizing ROI.
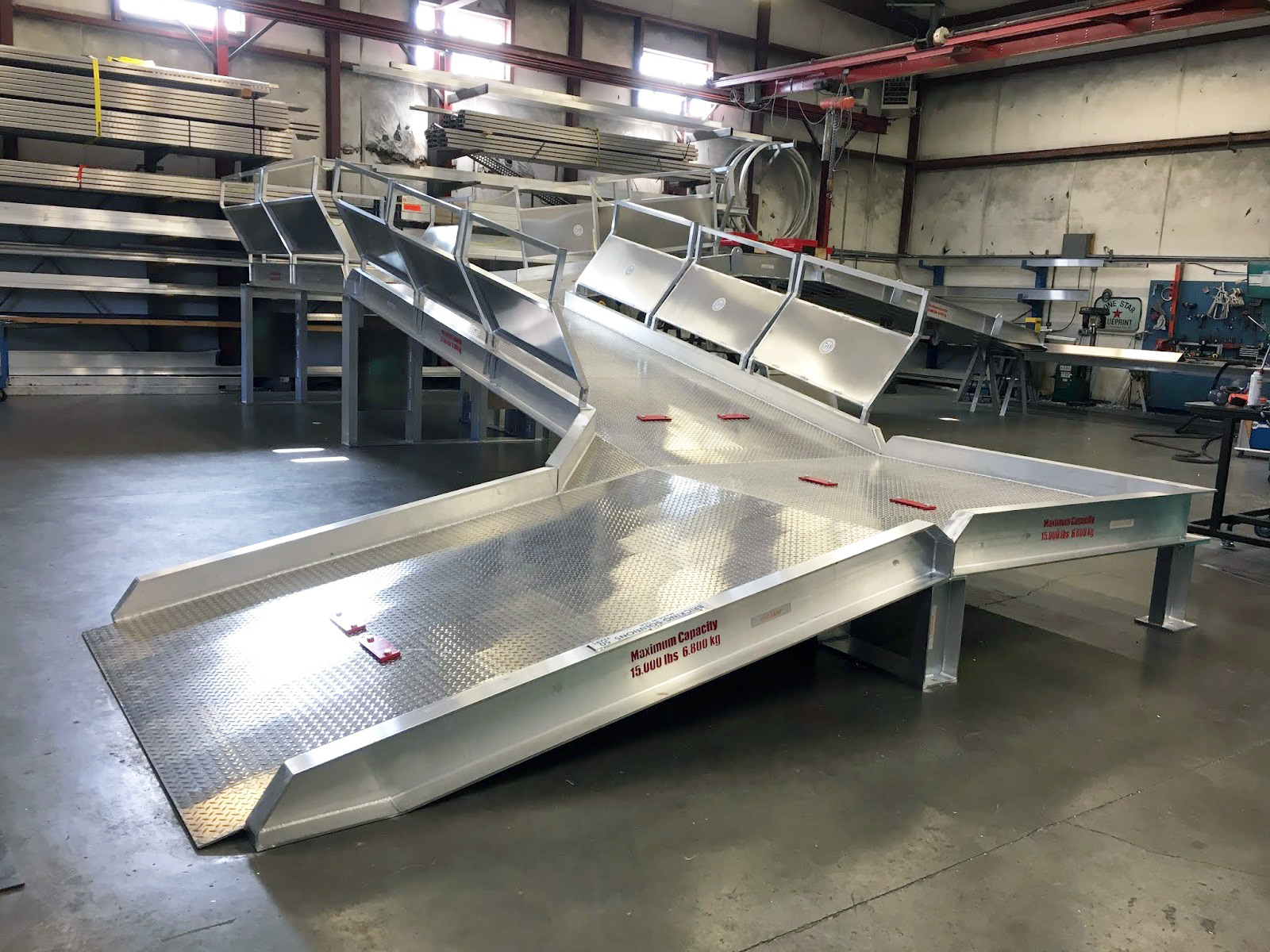